In 1859, Edwin L. Drake, a career railroad conductor, devised a way to drill the first practical oil well in the United States. Before Drake sank his first well in Titusville, Pennsylvania, people around the world gathered oil for centuries from seeps, places where oil naturally rose to the surface and came out of the ground. By the mid-1860s, new types of machinery brought about by the Industrial Revolution produced an increase in the need for lubrication products. This increased demand for oil led to Drake’s first successful oil well, in which he was able to produce a steady supply of 400 gallons of crude oil every 24 hours, a stunning amount in comparison to the meager output that could be collected from oil seeps (McNamara, Robert. “Edwin Drake Drilled the First Oil Well in Pennsylvania in 1859. An Unlikely Character Began the Modern Oil Industry.” About.com. Accessed April 18, 2015. http://history1800s.about.com/od/oil/a/first-oil-well.htm).
History of Gulf South Oil Production
As years progressed, the oil industry made its way to the Gulf South. On January 10, 1901, the first Southern well, Lucas No. 1, blew out in Spindletop, near Beaumont, Texas (Ramos, Mary G. “Oil and Texas: A Cultural History.” Texas Almanac. Posted on 2000-2001. Accessed April 18, 2015. http://www.texasalmanac.com/topics/business/oil-and-texas-cultural-history). As with the Gold Rush, everyone wanted a piece of the black gold, bringing about the continuous evolution of completion and production methods within the petroleum industry. This continued development aided the Gulf South by increasing the amount of oil being refined and consumed, transitioned the South from a strictly agriculture to increasingly energy focused market, and brought about many technological advances for the often perceived “backwards” South.
Early Methods Used to Produce Oil and Natural Gas
David and Joseph Ruffner, with their completion of a salt-water well that was drilled in Charleston, West Virginia in 1808, are credited with the first known completion methods (Hedrick, Charles. “Ruffner Family.” Rootsweb. 1884. Accessed April 18, 2015. http://www.rootsweb.ancestry.com/~wvkanawh/Early/ruffner2.html). One of the issues the brothers were confronted with was shutting off some of the lower concentrated salt-water sands, so they could produce higher concentrated salt water further down the hole. In an effort to overcome this problem, they engineered a makeshift device known as a “packer.” This device was made by whittling out two wooden tubes and wrapping the hole from end to end with twine, thus blocking off the lower concentrated brine and producing more of the higher concentration from a deeper depth. Essentially, the invention of this device allowed a well to be completed without different formation fluids mixing with each other by blocking off the undesired zone, and this invention eventually carried over into the oil industry (Beecher, C.E. and H.C. Fowler. History of Petroleum Engineering. New York. American Petroleum Institute. 1961. 745-751).
In 1939, many years after the introduction of packers, Paul D. Torrey introduced an important completion method known as “hydraulic fracturing.” This was first commercialized in 1949 by Halliburton Oil Well Cementing Company 6. The method was introduced to increase well productivity by creating deep penetrating fractures in the producing formation, thus increasing the well drainage area. The earliest variation of fracturing was acidizing, which was used to dissolve rock formations. The acid did not react with the hydrocarbons and improved the flow of reservoir fluids. Later, this method was replaced with hydraulic fracturing. In recent years, the development of the fracturing process has been an invaluable influence to the maximum productivity of oil from a reservoir.
Improvement of Equipment on Rigs
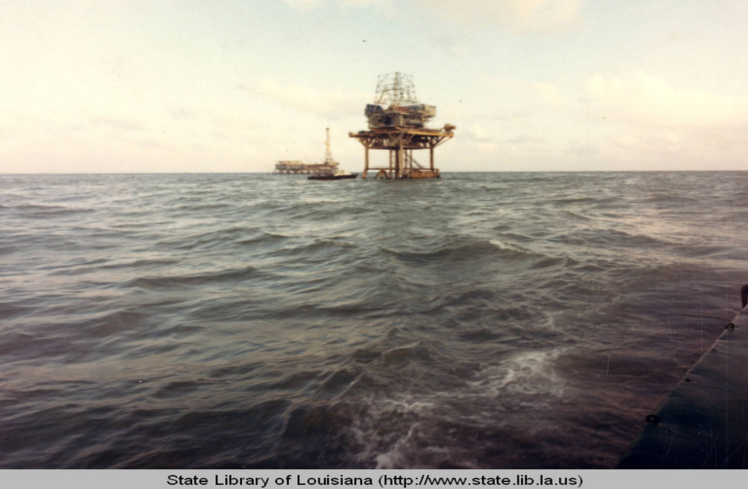
An oil rig in the Gulf of Mexico. Photo provided by the State Library of Louisiana.
Unlike today’s production techniques, original production methods rarely used scientific procedures. The main concerns focused on improving the equipment to get more oil out of the ground. Ten years after Drake’s first wells were established, however, pumping equipment became more conventional. Around 1880, the industry’s first major production-equipment improvement was the “central pumping power.” This replaced the costly maintenance of steam engines at each wellhead with the connection of steam-powered eccentric to jacks at each wellhead through shackle or rod lines. The next major changes did not occur until around 1900, when iron began to replace wood, internal combustion engines replaced steam engines, and rotary drilling gradually begin to eliminate the standard rig fronts that were made of wood to serve for both drilling and pumping. This change was almost mandatory because wells were getting deeper and the pumping pressures needed to be higher. The industry made a fast transition between 1922 and 1932, as mechanisms advanced with a wide variety of experimental equipment, and Petroleum Engineering was developed. The creation of the Petroleum Engineering field was not only important for scientific conclusions, but it also created an awareness for the need to regulate the oil. This viewpoint was significant for new and improving processes intended for environmental protection.
Environmental Concerns with Oil Production
Since hydraulic fracturing was introduced in the 1940s, many environmentalists criticized its method because it caused water contamination from the chemicals that were being used during the process. The controversy it brought about was the issue with disposing of the waste caused by the process, and was largely driven by the lack of chemical disclosure that occurred prior to the introduction of some state laws in 2008. To learn more about these fracking laws please see the following citation. (Horn, Steve. “ALEC Wasn’t First Industry Trojan Horse Behind Fracking Disclosure Bill – Enter Council of State Governments.” DeSmogBlog. May 2, 2012. Accessed April 18, 2015. http://www.desmogblog.com/alec-wasn-t-first-industry-trojan-horse-behind-fracking-disclosure-bill-enter-council-state-governments).
According to George E. King from Apache Corporation, fresh water contaminates are rare occurrences and happen due to the lack of proper laws in some states. Some examples of fresh water contaminates are found in abandoned and unregulated wells, unregulated pumping and mixing of the chemicals, and drilling in unregulated areas. In most cases, pressure-testing the cement, before and after completion, and with the monitoring of the 2008 fracking laws, has significantly reduced water contamination from that of the older methods used in fracturing (King, George E. Apache Corporation. 2012. “Hydraulic Fracturing 101: What Every Representative, Enviromentalist, Regulator, Reporter, Investor, University Researcher, Neighbor and Engineer Should Know About Estimating Frac Risk and Improving Frac Performance in Unconventional Gas and Oil Wells.” SPE 152596 1-80).
Another environmental problem brought about by production and completion methods is oil spills. For Gulf South states, an oil spill could be devastating to the Gulf Coast’s reefs and shorelines. Researchers Jennifer B. Culbertson and Christopher M. Reddy state that oil spills are particularly dangerous to Gulf South salt marshes. These marshes create natural barriers between land and water, and without salt marshes, Gulf South states become more vulnerable to natural disasters, such as hurricanes (Culbertson, Jennifer B., Ivan Valiela, Matthew Pickart, Emily E. Peacock, and Christopher M. Reddy. “Long-term Consequences of Residual Petroleum on Salt Marsh Grass.” Journal of Applied Ecology 45, no. 4 (2008): 1284-292. Accessed April 18, 2015. http://onlinelibrary.wiley.com/doi/10.1111/j.1365-2664.2008.01477.x/abstract). When an oil spill occurs in these areas, petroleum tends to sink to the bottom of marsh grasses, and this reduces mineral transfer from the ground to the plants’ roots. This directly affects the plant life, as many coastal reefs have been ruined and have taken many years to come back. Recent technological advancements, such as more reliable blow preventers, control systems, and transportation methods, have allowed oil producers to have fewer spills. When they have occurred, the clean up methods used are better than they have ever been. To see more on oil spills, see this chart on oil production tools.
Completion Methods
Since David and Joseph Ruffner’s invention of the first packer, completion methods have become more complex and reliable. When a well is completed before production, a casing design program must be run in order to prevent the wellbore from collapsing. Casing consists mainly of a steel pipe that is jointed together to make a continuous hollow tube along the majority of the length of the well. Once casing is suspended in the hole, the next step in completion is to pump cement slurry downhole, displacing the existing drilling fluids and filling the space between the casing and the actual sides of the drilled well. The casings’ main functions are to keep pressures balanced up to certain depths, which helps to prevent blow outs, block off formation zones that cannot be produced, and allow for faster production of oil from the reservoir. The newest method in cased-hole completion requires the casing to be run directly into the reservoir (“How Does Well Completion Work.” Rigzone. Accessed April 18, 2015. https://www.rigzone.com/training/insight.asp?i_id=326). In order to start production, the modern day packers, gamma ray well logs, and a perforation gun are lowered down to the hydrocarbon bearing zone via wire line. Once this zone is reached the perforating gun loaded with charges shoots holes in the sides of the well to allow the oil to enter the well stream.
Earlier hydraulic fracturing matured into what is now referred to as “frac-packing.” It is more beneficial to formations with high permeability. Shorter fractures could bypass damage in Gulf of Mexico wells that require sand control. These shorter fractures formed with water appear to be just as effective, whereas other conventional fracturing fluids damaged the permeability of the longer fractures. The damages that occurred were a result from shooting perforations into the formation and deposition of chemical scales from produced or injected water. The distance to which the damage extends from the wellbore is generally no more than a few feet (Cooke, Claude E, Jr. “United State Patent 6949491 B2-Methods and Materials for Hydraulic Fracturing of Wells,” Sep 27, 2005). Stimulation methods that are generally used for damage removal near a wellbore include limestone and sandstone acidizing and solvent injection, but occasionally these treatments are not successful, or their effectiveness quickly diminishes as hydrocarbons are produced from a well (Howard, George C., and C. Robert Fast. Hydraulic Fracturing. New York: Society of Petroleum Engineers of AIME, 1970). Hydraulic fracturing offers the benefit of removing damage to flow capacity near a well, which may be required in more remote areas, or areas that would be more costly to assemble the equipment. The end result is a higher yield of oil produced from a well in an effective and timely manner.
Production Methods
The current worldwide oil production has increased to 81,820,404 barrels per day (“Current Worldwide Oil Production.” Chartsbin.com. 24 Jun 2010. Accessed April 18, 2015. http://chartsbin.com/view/yp7). Constant improvement of production equipment is a major contributor to this large number. Rigs not only transitioned from wood to different metals, but also from land to floating production systems, tension leg platforms, sub-sea systems, and spar platforms. Floating production system platforms are versatile because they can either be floating semi-submersible platforms or drill ships, allowing oil companies to reach depths up to 6,000 feet. Tension leg platforms give companies 1,000 more feet of drilling, allowing them to drill well over a mile under water. The sub-sea system is exactly what its name implies, undersea pipeline systems transferring oil and natural gas after being drilled by a surface platform. Reaching the deepest depths, the spar platform allows companies to reach 10,000 feet. Its drilling platform is on top of a hollow cylindrical hull partially submerged 700 feet below the ocean’s surface. Even though it does not reach the ocean floor, its weight stabilizes the platform and the drill string stems through the cylinder and down to the ocean floor (Lamb, Robert. “How Offshore Drilling Works” How Stuff Works. 10 September 2008. Accessed April 18, 2015. http://science.howstuffworks.com/environmental/energy/offshore-drilling7.htm).
The increased need to reach deeper depths and to produce the hydrocarbon reservoirs brought about advancements in pumping technology. As a result, the methods used to get more oil out the reservoir have become more complex. Drilling at a deeper depth brings about increased pressures and higher temperatures, which results in the constant change and maintenance in the drilling fluid being used. In order for the drilling fluid to circulate continuously through the wellbore, triplex pumps and duplex pumps are being used to continuously cycle the fluid. As a direct result, blowouts are prevented, drill pipes becoming stuck occur less often, and wellbore stability is maintained in areas where the casing does not reach. Drilling to deeper depths has allowed for a sharp increase in oil production because oil companies are able to go to areas that could not be reached in the past.
Since target depths are being reached faster than ever, the reservoir production methods have evolved with it. In the early days, oil companies would rely sharply on the primary recovery method. Although this method allowed for the production of oil, its results were not great. The method is based on the pressures that exist in the reservoir, which push the oil to the surface, yielding only ten percent of the oil. However, as time went on, petroleum engineers and geologists found newer ways, called the “secondary” and “tertiary recovery methods”, to get more hydrocarbons from the reservoir being produced. The secondary recovery phase uses water or gas injection into the reservoir to displace oil, making it much easier to drive it into a production well bore (“How Does Well Completion Work”. Rigzone. Accessed April 18, 2015. https://www.rigzone.com/training/insight.asp?i_id=326). Lastly, the tertiary recovery, or enhanced recovery, involves injecting other gases, uses thermal energy to reduce the viscosity allowing more flow, and chemical injection to increase the effectiveness of water flooding (Burgess, Luke. “Enhanced Oil Recovery” Energy & Capital. Feb 28th 2006. Accessed April 18, 2015. http://www.energyandcapital.com/articles/enhanced-oil+recovery-gas/148). This stimulates the flow of the oil and produces remaining fluids that were not extracted during primary or secondary recovery phases.
Conclusion
Oil and gas production in the Gulf South has brought about many positive, and some negative, benefits. The introduction of oil production in the early 1900s created an ever changing demand for newer machinery and equipment and initiated a rat race for the land where oil companies wanted to drill. This increase in demand has started a trickle-down effect throughout history in reshaping our environment and landscape. Land that was once used for farming is now being used to drill and produce oil, our gulf coast is littered with old platforms, and pipe lines cover the sea floor to enable better transportation of the produced hydrocarbons and natural gases. Without the discovery and advancement of the methods used today, our economy would not have evolved so quickly. Many things, from the cars we drive, to the energy we use to run our houses, would not have been accomplished without some natural resource as a basis for our infrastructure. Some may argue against this statement. However, it is clearly seen around the world today that natural gas and oil are becoming a precious commodity due to over-consumption and a high demand to increase the technology used in almost every facet of industry.